Expansion at Axess
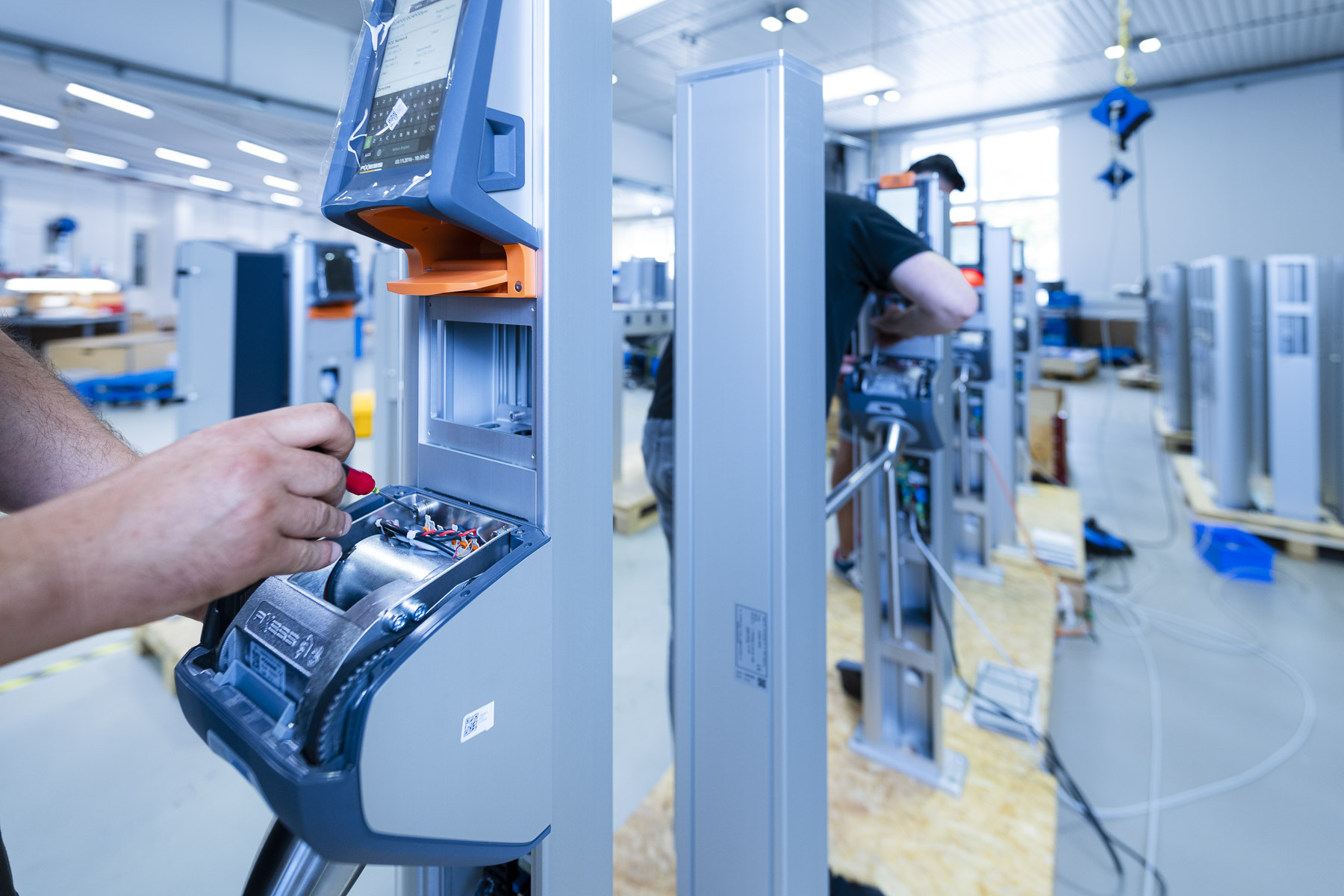
For 24 years now, Axess AG´s turnover, number of employees and floor space have been growing steadily. While in 2012 the company had 156 employees, now 400 people worldwide are working to provide digital access solutions with integrated software products in five different business areas. From ski resorts, football stadiums, fair and exhibition centers, leisure parks or tourist attractions, they all need a system to organize ticket purchase as well as access digitally.
Within the last five years, the production plant in Innsbruck has been constantly expanded and extended. "Despite the pandemic and economically challenging times, sales have increased every year. This year, it was even possible to take over the entire building of a former printing company. As a result, the factory now has 1,800 m2 more floor space available," says Michael Steinberger, factory manager in Innsbruck. By making dynamic adjustments to the changing market conditions after the first lockdown, Axess was able to quickly pick up speed again. The accelerated urgency to digitize gave rise to many new projects worldwide. This is of course reflected in terms of production.
From now on, all hardware will be manufactured in the new building in Innsbruck. It also offers storage rooms and sufficient space for logistics. The module and ticket production remains in the old part of the factory and could be enlarged by 130 m2 by relocating the hardware production. This was also necessary as the space available for production was becoming increasingly cramped. Already 4 years ago, the 2-shift operation in ticket production has been changed to a 3-shift operation in order to meet the requirements of the growth in sales. A total of 2,245 access points, 540 self-service ticket machines and 24 million tickets are produced per year. With a total area of 6,700 m2, the Axess factory will manufacture all Axess products from July.
Of course, the number of employees also increased over time. Whereas at the beginning there were 18, in 2012 already 60, and now the Tyrolean site already employs 105 people. Thus Axess has grown into a popular employer, all employees are from the area and have been working at the factory for a long time.
"We are very proud that we can deliver quality "made in Austria". Our customers and business partners appreciate this very much, the quality is undisputed better than from suppliers in cheap third countries. So we are a 100% Austrian company which manufactures 100% in Austria" says Markus Weyrer, Sales Director for the ski division in the DACH region. In Tyrol, the systems have already been in proven for a long time. For example, at the Patscherkofelbahn, the Nordkettenbahn, the prestigious ski resorts Arlberg, as well as the ski resorts Seefeld Rosshütte, Bergeralm, Glungezerbahnen or Axamer Lizum.
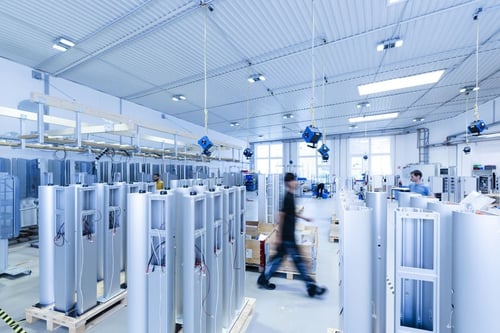
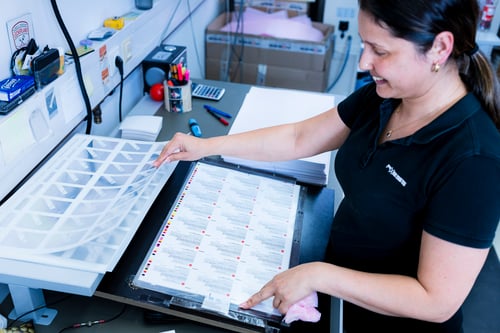
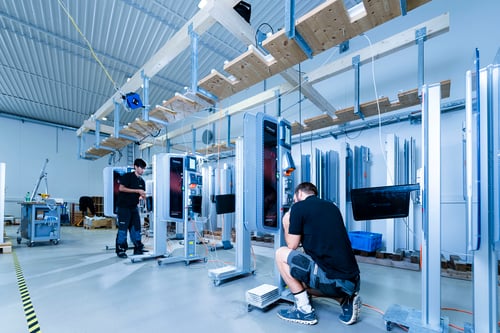
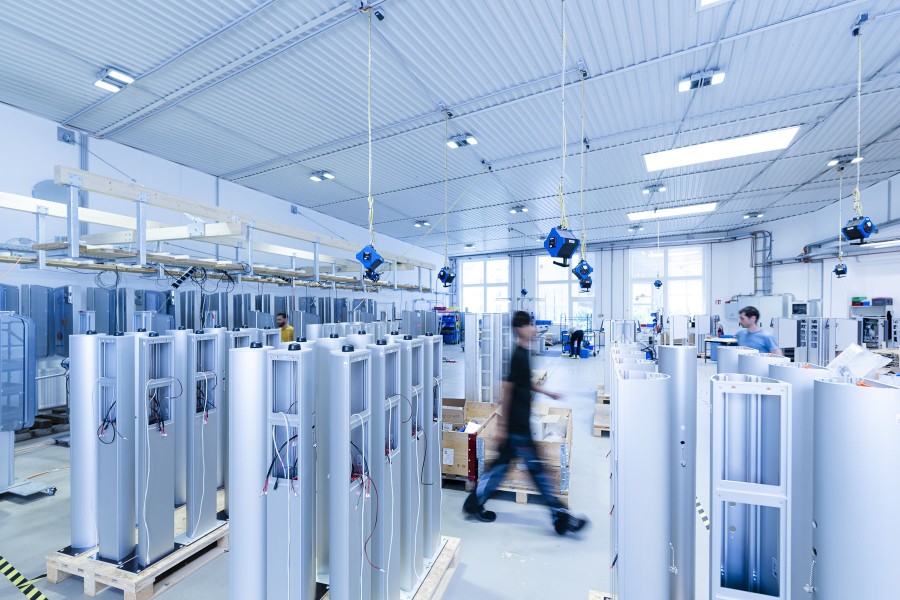
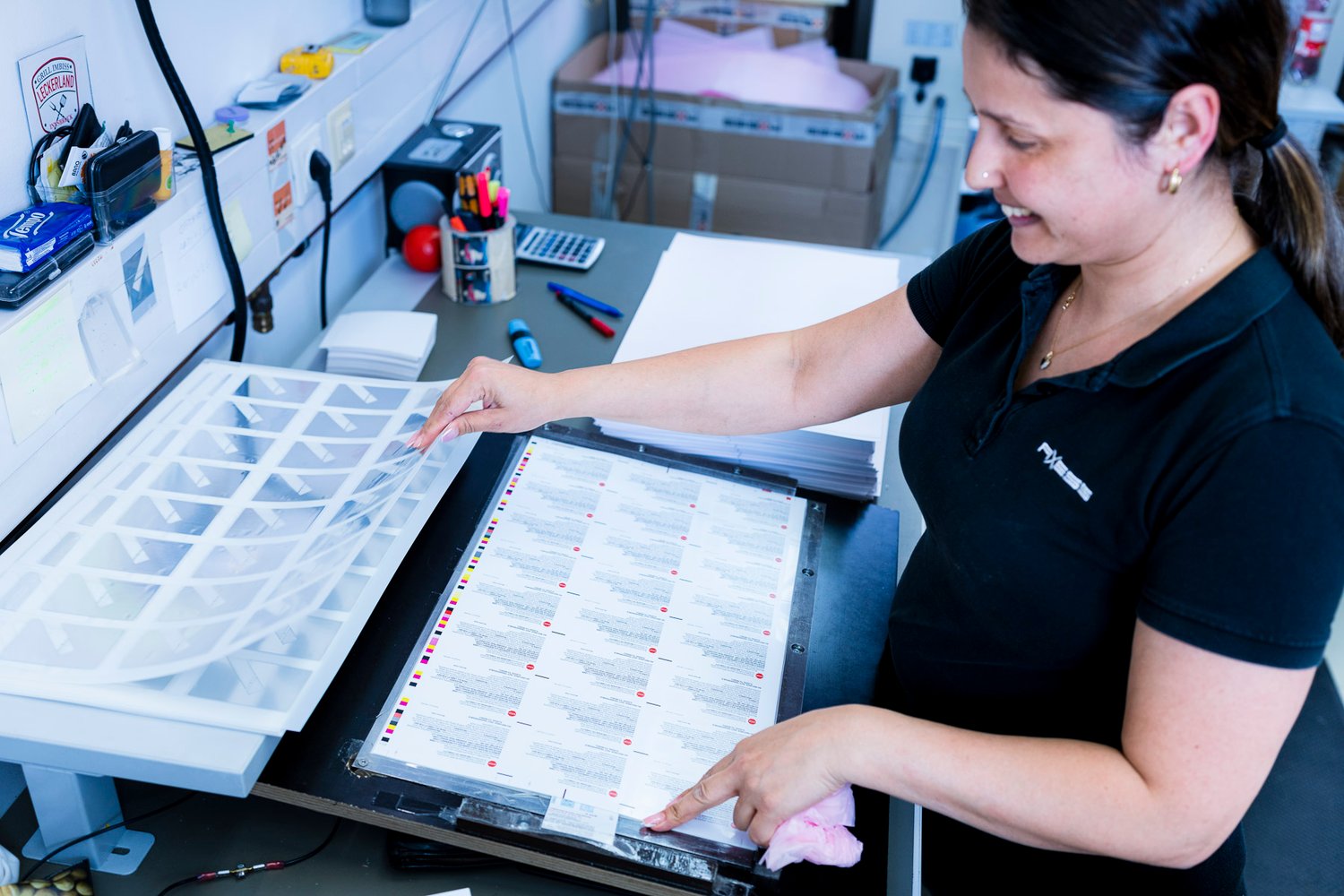
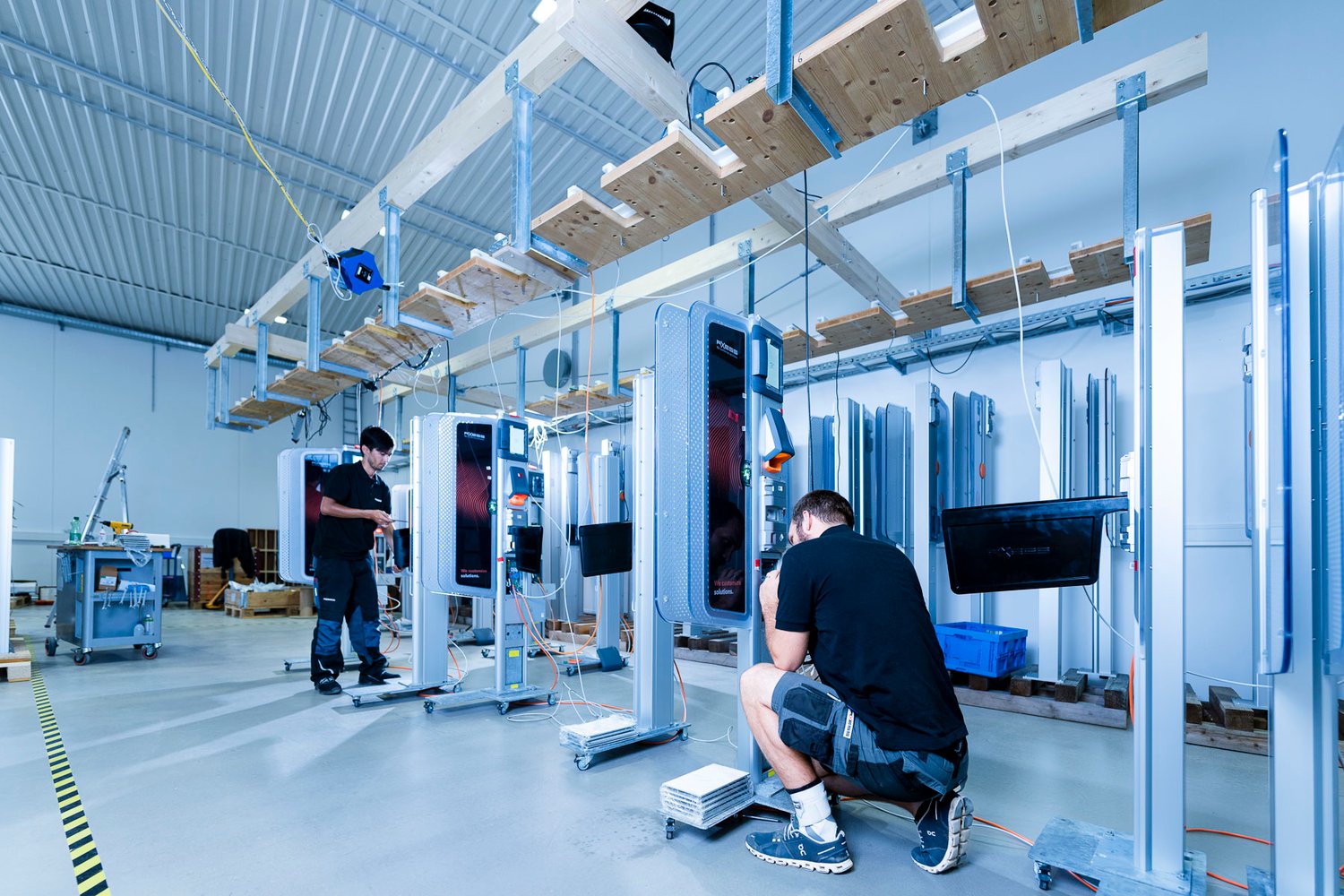


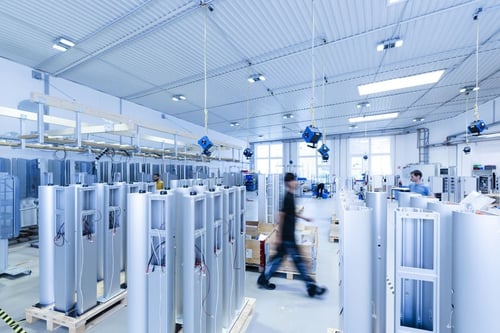
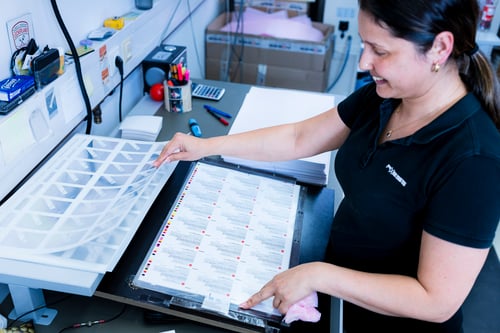
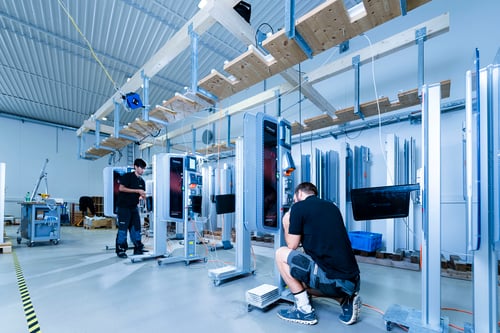



News
Latest Projects, Events, Research & Development activities and News from the World of Axess.
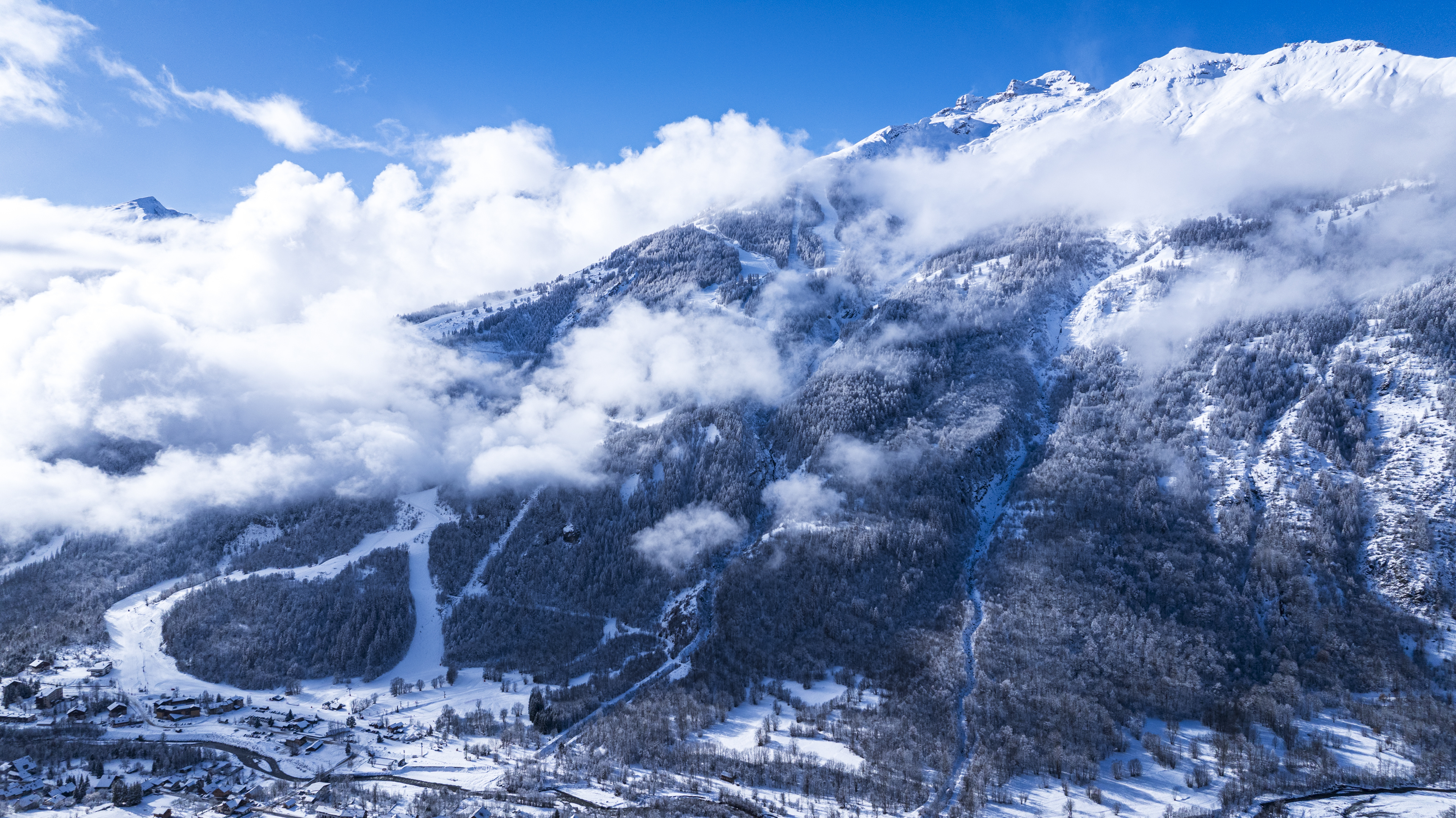

A successful transition for Pelvoux-Vallouise
By replacing its installations with a global solution from Axess, the ski resort has opened up new prospects that will enable it to optimize its revenues in the long term.
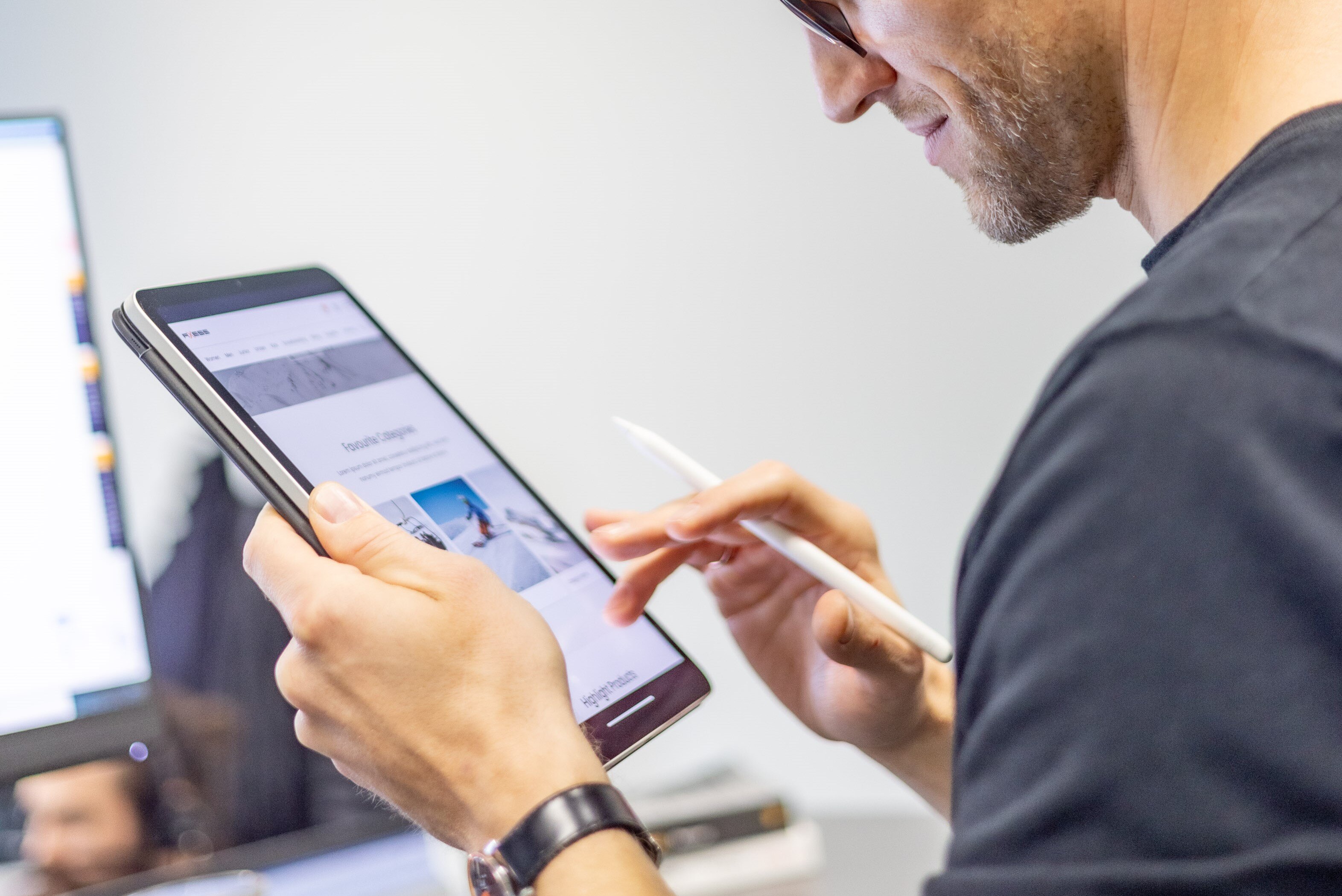

Your solution for data management in the leisure industry: Axess SMART SOLUTIONS
With Axess SMART SOLUTIONS, data analysis, intelligent systems, and AI are used to drive growth, optimize processes, and strengthen market position.
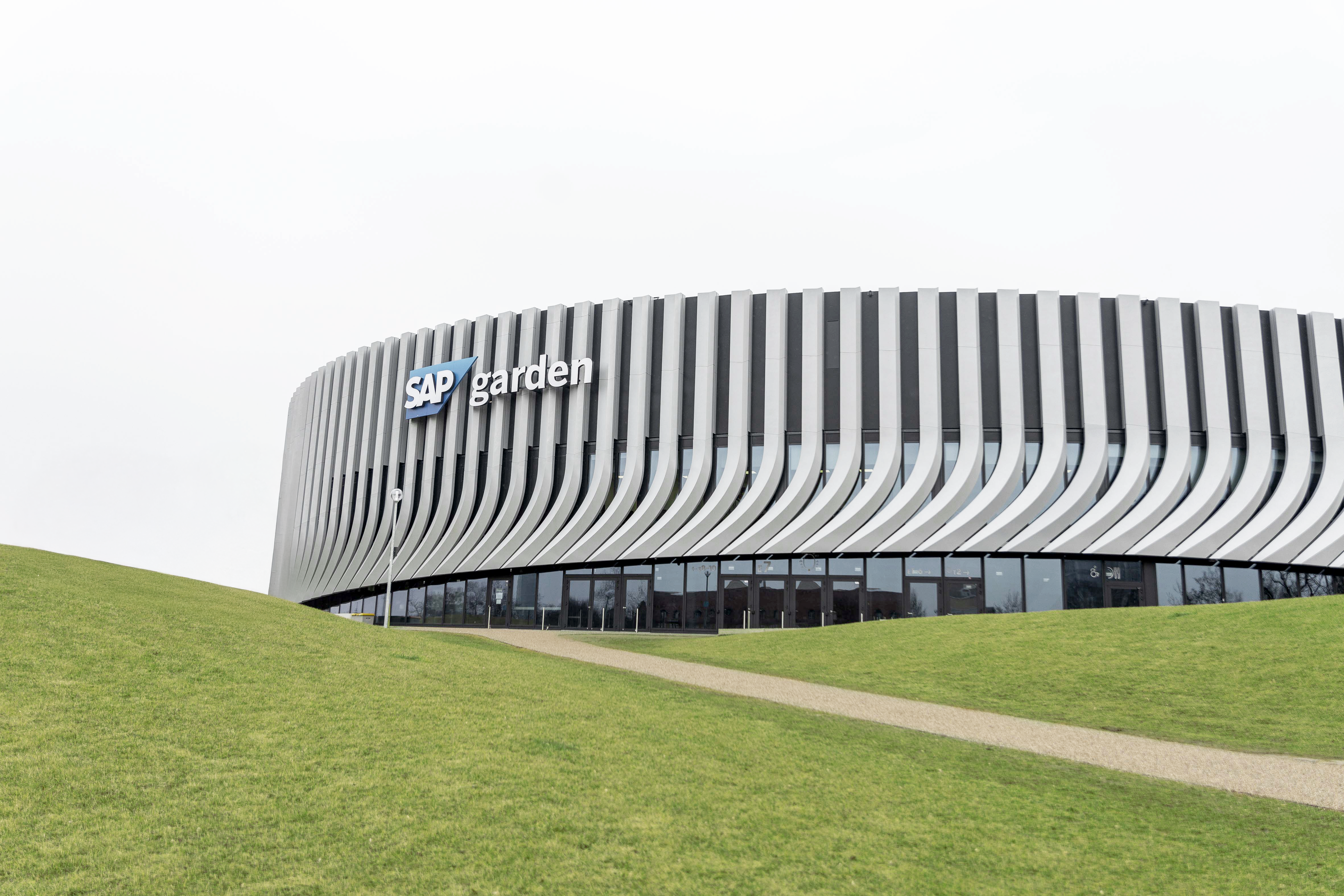

SAP Garden: The ultimate year-round hub for pro and amateur sports
The SAP Garden in Munich is a state-of-the-art sports venue which has integrated Axess’ high-performance access gates for a seamless experience.